This paper is about
how a consortium of five Japanese companies (COJAAL: Consortium Japonais Pour L’Autoroute Algerienne) is undertaking to build a 399 km, six-lane, limited-access highway across northern
Algeria. The paper
starts with the bidding process,
the evaluation method and the structure of contracts that govern the construction of the project
on a design-build basis. Since the contractor is allowed to alter, and
therefore is responsible for, highway routing to a certain extent, the paper describes how this discretionary power was exercised to determine the final location
of the highway. The paper then goes on to outline organizational setup, physical and design parameters, procurement and logistics,
and construction execution plans. As of
February 2009, the contractor
is about 29 months into the project,
whose duration was originally set at 40 months.The
paper highlights events and/or issues that have had time impacts since its commencement in September
2006. Some sections of the project
have faced major landslides.Other sections
are being impacted by a shortfall
of critical materials such as crushed gravels for pavement. The contractor also experienced complications from having
to build a project to the French
standard when natural conditions in Algeria do not necessarily lend themselves to the French standard. Sourcing and mobilizing labor from out-of-the-country markets
in sufficient numbers and having
them work efficiently
on a stretch of construction sites extending over hundreds of kilometers have added to the task of coordination and control. As such, the paper represents an interim report on, and a case study of, managerial and technical challenges that an overseas
project of this magnitude and scope can present to the contractor, as well as approaches that can be taken to meet such challenges.
KEYWORDS: highway construction, design-build management, construction standards
1. INTRODUCTION
In September 2006 a consortium of Japanese contractors (Cojaal: Consortium Japonais Pour L’Autoroute
Algerienne) signed a ¥5.4 billion
design-build contract for a 399 km eastern section
of the Algeria East-West Highway, one of the largest
civil construction projects
ever to be undertaken by one entity in the history of the Japanese
construction industry.
The award
was
a
result of international biddings conducted by the Algeria Public Works Ministry
in January 2006 to build out a contiguous 1,200 km
East-West Highway from the Moroccan
border to the Tunisian
border. The
Ministry
divided up the Highway into three sections of approximately
equal size, with Chinese contractors coming out as the winners of the western and central sections. Of the six bidders who competed for the eastern section, Cojaal
bid the highest. Bid evaluation assigned 60 points to technical and 40 points to financial. Cojaal succeeded in tipping the scale largely on the strength
of technical merits that it earned for a crash construction program utilizing global
positioning systems, and contingency planning for the earthquake hazard.
Figure 1.1 gives
an
outline
of
the
Project,
while
Table 1.1 details
the structure of contracts
as well as
how
each contract defines contractor’s
design-build responsibilities. Of particular note is the contractor’s right to propose alternative routes
over large stretches of the Highway.
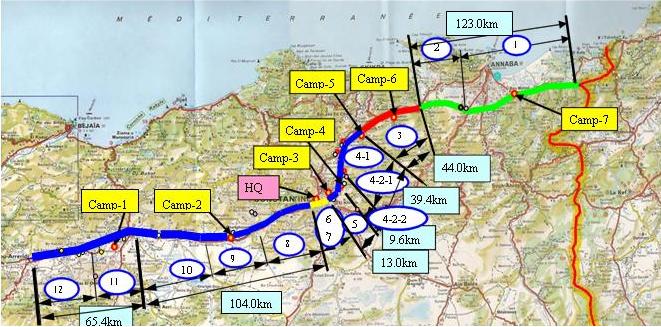
Figure 1.1 Project Outline
Table 1.1 Structure of Contracts
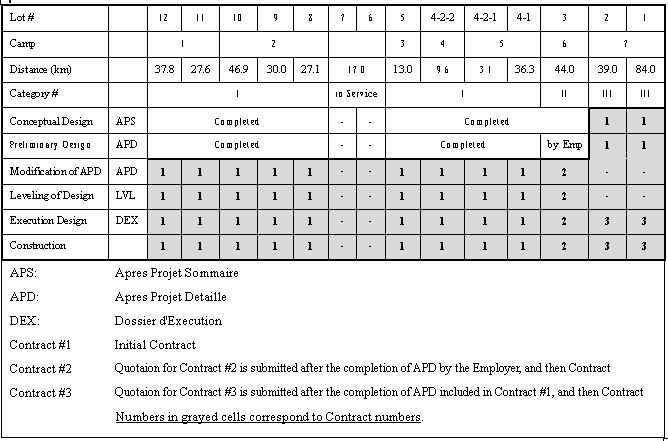
As of February 2009, Cojaal is approximately 29
months into the 40 month project. In what follows, the paper describes how Cojaal set itself up to handle
this enormous undertaking, and what it encountered once the project got under way. As such, this is an interim report on managerial and technical
challenges that an overseas
project of this magnitude and scope
can present to the contractor, as well as
approaches that can be taken to meet such challenges.
2. HIGHWAY ROUTING
The ¥5.4 billion contract amount was introduced at the last stage of contract negotiations with the Employer as a
cut-off point for the aggregate payments that Cojaal is entitled to receive inexchange of completing a yet-to-be-designed Highway whose routes are subject to change.
The only exceptions are cost
and time associated
with variation orders,
force
majeure,
and
other
causes attributable to the Employer.
Preliminary studies by Cojaal revealed that moving
the Highway from its initial route through the coastal
mountains to
the edge of the coastal plains northward would eliminate tunnels
as well as high
bridges across ravines. These cost savings,
however, needed to be weighed against
impacting
towns and villages
along the alternative routes and having to spend time devising,
negotiating and implementing
mitigations.
In anticipation of this, Cojaal negotiated a special contract provision that compensated
the contractor for time and cost arising out of extended delays in
obtaining approvals.
When Cojaal accepted this “price ceiling,” it essentially took it upon itself the challenge
to choose
Highway
routes and to develop
subsequent design
details such that, barring force majeure and other
exceptions, the Highway
can be executed on time
and project cost can come
in below the price ceiling.
3. PROJECT EXECUTION
This Chapter summarizes how
the Project
was initiated and managed at site, highlighting issues
of time management as well as quality control.
The members of Cojaal recognized
that key success factors in this regard
are procurement and logistics (P/L) and design
management (D/M).
3.1 Organizational
Setup
Project
organization adopted
involves seven site offices, called “Camps,”each of which
is to construct a section of the Highway that varies
in length from 12.7 km to 123 km. The Headquarters (H/Q) coordinates, controls and integrates the activities of the Camps as shown
in
Figure
3.1.
Each Camp internally replicates the functions
that H/Q has, such as Contract Administration and Design Management.
Design
within the scope of Cojaal is outsourced
to internationally recognizedm design firms. The
design process is managed by staff dispatched from the members of Cojaal.
3.2 Construction Execution
The Campsexecute construction of the assigned work scopes independently, based on work budgets
and programs that have been agreed upon at meetings presided by the H/Q.
With the exception of Camp 7, each Camp is
operated by one member of Cojaal. For
instance, Camps 2 and 4 are operated
by Kajima Corporation
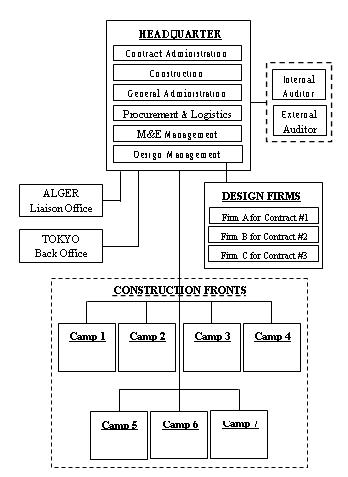
Figure
3.1 COJAAL’s Organization
alone. This setup gives each member company
managerial autonomy, allows aggressive application of proprietary technologies, and most importantly, provides
a strong incentive to achieve good results for the company,
contributing
to Cojaal’s overall success.
As Camp 7 was to commence last, it is operated by
an internal
joint
venture
where
the
members of Cojaal can pull together their experiences from their
own Camps and expedite work progress.
3.3 Procurement and Logistics
Timely procurement of plant, equipment and major materials is a prerequisite to on-schedule
work
progress.
3.3.1 Plant
and Equipment Procurement
Since aggregates, cement concrete, and asphalt
mixtures shall be manufactured by Cojaal, all necessary plant and relevant equipment were globally procured early on. So were earthwork
heavy equipment, passenger vehicles and other
common
equipment.
In order to meet a demanding time-schedule, huge
volumes of cargo were rushed in the initial
stage to the Port of Skikda,
the closest and most convenient
port of entry Table 3.1 exhibits a procurement schedule of such major plant and equipment which were
purchase-ordered
to vendors during the first seven
months immediately after signing the contract. The countries of origin range from Japan, North America,
Europe to South East
Asia Table 3.1 Procurement Schedule
of Major Plant &
Equipment during the first Seven
Months
The total volume of plant and equipment shipped to
Algeria from various countries amounts to
110,000FT
during
this
first seven months,
out
of
230,000FT during 28 months until December 2008. The value of the
first
seven-month procurement exceeds 20 billion Yen, or 220 million USD.
The P/L
mission has been carried
out with diligent preparations and particular care taken to:
1) Purchase-order to plural vendors a single item at
a time to procure a large quantity in short period.
2) Manage
delivery of the items to warehouses
at original ports to effectively utilize
deck spaces of cargo vessels
3) Call
well in advance cargo vessels bound for or via Algeria, whose availability is quite
limited.
4) Make
up complete shipping/import documents to facilitate customs clearance.
5) Hire effective stevedores; experienced custom
brokers; and inland
forwarders to unload and transport the cargo out of the port in a timely manner.
6) Communicate well within the P/L team located both at H/Q, the consignee; and at Tokyo back office,
the shipper.
3.3.2
Materials Procurement
An initial assumption that major materials such as
aggregates, cement, reinforcing bars, concrete pipes, and
bitumen, etc., can be procured easily from local sources turned out to be inaccurate:
1) Aggregate
The planned Highway route provided distant
views on both sides of a number of mountains
being actively quarried, which led Cojaal to attempt to purchase from the operators of those quarries the necessary quality
and quantity of aggregates. This effort
was
given
up due to disagreement over the conditions
offered by the operators.
The second and adopted option was
for Cojaal to operate crushing plants at quarries
and produce the aggregates. However, some quarries turned out
after
some trials
to
produce limestone aggregates that did not meet the specifications in terms of Los Angeles Abrasion Test results.
The engineers
from the Camps and the P/L team collaboratively explored satisfactory quarries, and the last necessary quarry was identified only recently. This time-consuming quarry hunting has resulted, in part, in the procurement of a large
number of crushing plants as shown
in Table 3.1.
2) Cement
Since Algerian mountains are constituted primarily of limestone, ERCE, a government
agency, operates a number of cement factories. Although the quality is satisfactory, the quantity is not enough. As a result, cement lorries dispatched from the Camps routinely wait for cement loading
for several hours in a line at the
factories. Consequently, a cement
lorry can
makeonly one
trip for cement transportation a day, leading to less
stock in
silos than was planned.
This situation aggravates
in summer time when
production drops due to the “Vacance,”
similar to what happens in Western Europe. Some busy Camps have
responded
by stockpiling
cement in “Ton
Bags” in well
conditioned warehouses two months before summer vacation starts.
3) Reinforcing Bar
The specifications for the rebars are in accordance with the French standard,
which is unfamiliar to non-European suppliers. Thus, the number of foreign
suppliers that Cojaal can use
is limited.
It was fortunate that an international steelmaker operates a steel mill in Algeria, and that rebars using the French standard
were available locally through their official distributors.
The problem
was the handling of the rebars at the distributors’ warehouses. Poor inventory management has made it difficult to identify
rebar specifications such as
strengths and diameters.
Thus, the P/L
team
was
forced
to
procure
specified rebars from reliable Italian suppliers
at the beginning.
Similarly,
Cojaal
has
experienced
problems
with many other materials that were locally procured.
3.4 Design Time Management
Design time management is critical to the overall management of time for a design-build
project. When design is not finalized and fixed on time, subsequent activities
such as
procurement and construction can not be carried
out
according to schedule. Benefits of fast track or phased
construction often sought in the design-build scheme are
thus predicated on successful time management of the design process.
3.4.1
Design Information Flow
Figure 3.1 also shows Cojaal’s design organization. H/Q’s design management team and Camps’ design
team
collaborate with outside design
firms.
The Employer also hires his own design consultants
as “Technical
Advisor” and “The Engineer.” They
are the counterpart of Cojaal’s design
management team.
Figure 3.2 exhibits the flow of design information
exchange among the design-related organizations in case of LEVELING and DEX. The LEVELING
is the matter of “Technical
Advisor” and the DEX is of
“The Engineer” in the
Employer’s
organization. The design is finalized when the DEX is approved.
The DEX approval procedure is summarized
in
Figure 3.3. The
DEX
can
be
approved
in
a
minimum of 15 days if the Engineer
does not find in the
submitted DEX draft any major deviations from
the Employer’s requirements in the Contract
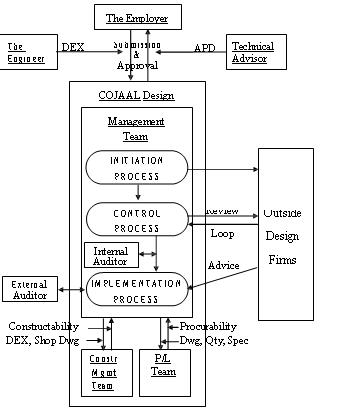
Figure
3.2 Flow Diagram
of Design Information for
LEVELING
(APD) and DEX
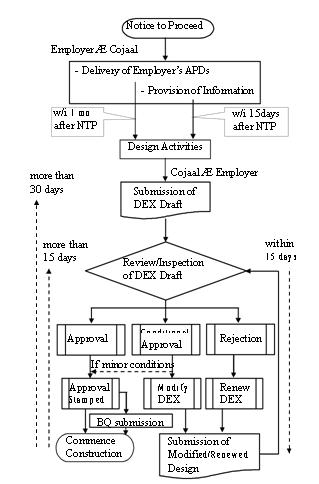
Figure 3.3 Flow Diagram of Approval Procedure
for
DEX
3.4.2 Difficulties in Design Time Management
Cojaal
has found it difficult to manage design time in
this Project. Uncontrollable and/or unexpected
events and
circumstances have affected the design process,
in more ways than Cojaal
ever expected. Approvals
of the designs presented to the Employer (the Engineer
and Technical Advisor) were anything but timely
or forthcoming.
The difficulties which Cojaal
has faced include:
1) Limited availability of original APSs & APDs,
2) Sparsely located original bore-hole
logs,
3) Environmental restrictions unknown to the
Bidder (prospective Design/Builder),
4) Technical Specifications particular to this
Project,
5) Unfamiliar standards (the French standard) frequently referred
to in the Specifications,
6) Inconsistency time-to-time in the Design
requirements and preferences,
7) Lack of prompt
Employer
responses
to
the Contractor’s submission,
8) Magnitude of the Project
9) Design Firms located outside
Algeria
10) Disagreements with
the
international design firms
11) Reconciling construction requirements with design requirements
12) Pursuit of cost effectiveness in the design phase under the price ceiling
13) Scarcity of experienced in-house design mamagers
14) Ruling French language
3.4.3 Design/Build scheme : from the Contractor’s View
Textbook arguments for and against the D/B scheme
typically look like the following:
1) The Contractor
can incorporate its innovative
technologies and constructability in the design,
leading to reductions in cost & time,
2) Overall project time can be reduced to
the extent that “Fast
Track” or “Phased Construction” is possible,
3) “Checks and balances”does not work well between the designer and the contractor because both functions are integrated in one entity,
4) The Employer needs to take strong control of project expenditures so as not to allow the cost
to exceed the budget, and so forth.The experiences by Cojaal, however, suggest
that benefits of design-build can vary greatly depending on
the following circumstances:
1) The
design/builder proposing to
utilize its innovative technologies for time/cost reductions often meets with resistance from outside design
firms because the latter are afraid of liabilities
that may
arise from
adopting such innovative technologies.
2) Design
time management is a complicated task, often leading to delays in design progress. In
such cases, the benefits
of fast track or phased construction are elusive.
3) The Employer has the ultimate
right to approve design and
construction, meaning
that
the Employer’s review and/or approval
rights affect all
activities of the design/builder. The degree to
which this relationship
can
work
to
slow
or
expedite project progress
may exceed contractor
expectations.
4. CURRENT ISSUES IMPACTING TIME
Of the events that impacted on-site
work progress since construction commenced, two things stand out: landslides and a shortage of aggregates.
4.1 Landslides
Part
of the Highway traverses an extended terrain characterized by limestone-marl formations. Cojaal
did not anticipate the degree to which
partially-weathered marl in this
area
is susceptible to
landslides. After excavation started on the tunnels
in this section of the Highway, construction stalled
in the face of extensive landslides around tunnel entrances and where
hillsides
were
cut
for
the project.
Mitigation measures included
moving the location
of tunnel entrances, constructing embankments or
driving long piles that can hold the weight
of marly
formations on the slopes above, and installing drainage
channels through the marl.
4.2 Shortage of Aggregates
Production of
aggregates
suffered not
only from difficulty of finding
suitable quarries but also from restricted supplies of explosives. The latter was
due to strict controls on the distribution of explosives for security reasons: regulations require
that any transportation of explosives
from the only source available near the western section of the Highway to the quarries be attended by armed official guards,
and all explosives be used up while the guards are in attendance
at the quarry.
This places severe constraints on the production of concrete and crashed
gravels
for
pavement,
and
limits the amount of blasting for tunnel excavation.
Cojaal is applying
for
a
special
permit
to
build
explosives stockpiles. The location of such storage facilities is still
being negotiated.
4.3 Construction Standards and Specifications
The Employer has adopted construction standards and specifications (CCTP) that are conceived along the French standard. CCTP not only
requires testing methods and performance measures that are unfamiliar to Cojaal,
but also imposes restrictions that
are often at odds with local conditions
in Algeria.
As a case in point,
CCTP discourages the use of limestone aggregates in the surface
course asphalt mixtures when in fact the only aggregates locally available in large enough
quantities are of limestone. The issue is insufficient hardness of local limestone.
As a result, a solution being proposed by Cojaal is to mix blast
furnace slag or hard
sandstone with
limestone aggregates to improve the abrasion/corrosion resistance.Cojaal continues
to
encounter
situations
where
it
finds
CCTP impractical or uneconomical, given
local conditions. Cojaal’s approach has been to devise
alternative means or methods that Cojaal deems to
be “equivalent,”
and
to attempt to convince the Engineer to adopt them. Cojaal is assisted in this
effort by a committee of experts formed
in Tokyo that regularly convenes
and
advises
on
technical
solutions.
4.4 Labor Management
Cojaal found that the Employer often had issues with the qualifications of subcontractors that Cojaal had chosen
to bring
in from foreign countries. It was also time-consuming
to
obtain
visas
for
imported labor.
Supervising groups of labor that are positioned far apart along the Highway has proven to be
demanding especially when the distance
involved can be 50 km or more. Workers who are rushed to move
between work locations using two-lane local highways
or partially completed roads are prone to engage in unsafe driving
practices, which have led to some fatal
accidents.
The task of on-site labor management
is often compounded by an
apparent lack of
sufficient supervisory capacity
on the part of the Employer. On-site
progress suffers and confusion ensues when
the Employer does not dispatch
someone to either attend
the testing or approve construction work that is ready for inspection.
5. CONCLUSION
Cojaal signed
on the ¥5.4 billion contract
for the Algeria East-West Highway with a full realization that
it
was crash
construction program
on
an
unprecedented scale. While
it may not have been typical for a design/builder to commit to a fixed sum
when the design was so incomplete, Cojaal regarded
the design-build features – including contractor’s
discretionary right to alter the Highway routes – as a lever with which to make the Project work as a
business proposition. It was a judgment call based on much analysis at the time and strong commitments from its members.
Working with a foreign government Employer on a
design-build project based on unfamiliar construction standards and specifications has so far been more than challenging; yet the members
of
Cojaal are bringing all their expertise and resources to bear
on the Project in order to succeed.